CMMS Data Transition and Quality Assessment
Client: Energy service company
Asset: 2 offshore production platforms
Project Objective: To source a new “fit for purpose” CMMS and migrate all existing data to the new platform ensuring no impact on the client’s maintenance schedule
Project Duration: 6 months plus ongoing support
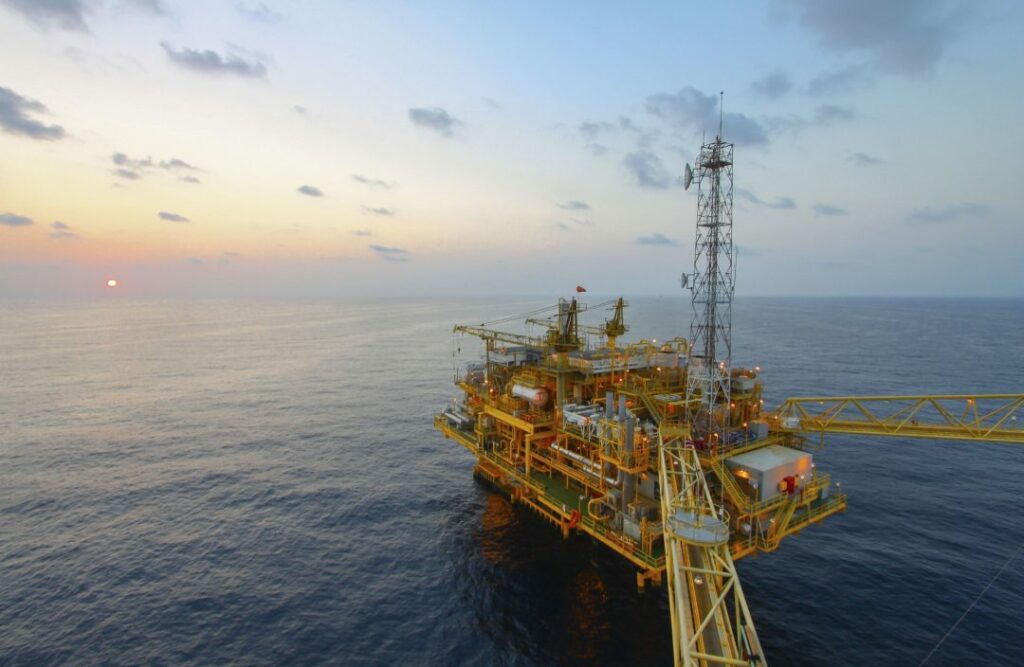
Why were we contracted?
After obtaining control of two offshore production platforms that were in the decommissioning phase of their lifecycle, the client was looking to transfer their data from the existing CMMS used by the previous operator to a new CMMS platform.
ABL were tasked with sourcing a new “fit for purpose” CMMS and transitioning the existing data from the current CMMS to the new platform, ensuring that there would be no impact to the current maintenance schedule.
This is a service ABL specialise in, and not something a company would normally undertake themselves without the correct level of knowledge.
Challenges faced by the client
- With so many variations of CMMS on the market, the client required direction in choosing which system would work best for their operations
- Because the data already existed in the CMMS from a previous company, the client was unaware of what state the data would be in, how feasible a ‘Lift and Shift’ style approach to the new CMMS would be and what data they would need to transfer across
- The client had to ensure that maintenance routines would continue to function during the CMMS transition period in order for work to continue to be completed
- It was essential that the current maintenance history was transferred to the new CMMS once it is live
What we did
- Having worked with many different CMMS systems, our experts advised a cloud based CMMS as the most suitable solution for the client’s desired price range and functionality, due to its adaptability into oil and gas specifications
- Working with the client and the CMMS provider, we created, customised and configured the system to accommodate their business processes and ensured a smooth transition with minimum impact to the end users whilst maintaining user familiarity with the data and layouts
- Performed a full quality assessment on the existing data to ensure a ‘Lift and Shift’ approach was possible with minimal change to the core data
- Implemented one of our standard ‘go-live’ processes, which tracks and records all data movements such as work order completion and corrective maintenance creation made during the transition, enabling us to update the new CMMS once it has become live
- Trained the client’s maintenance team in the new CMMS platform via online workshops
How did our work benefit the client?
Maintenance schedule remained functional
The asset was kept 100% functional throughout the CMMS transition period meaning there was no disruption to the client’s existing maintenance work schedule
Ensured client confidence in new CMMS data
Delivered cleansed data for the client’s assets which allowed a smooth decommissioning process
Real time visibility of data
Created a set of dynamic system KPI’s and graphs which demonstrated compliance and assisted the users in understanding the current state of their maintenance
Optimised costs
Data in the old CMMS was reflected accurately in the new CMMS and therefore could be managed appropriately to assure reliability and optimise costs
Compliance with audit regulations
The work we completed allowed the client to successfully complete their transitional decommissioning audit
Improved competency of workforce
Provided the workforce with training in the new CMMS platform, saving the client money on separate training courses