Development of a maintenance management regime (CMMS build)
Client: FPSO Operator
Asset: FPSO
Project Objective: To deliver a digital twin of the maintainable physical equipment and their functional locations within the CMMS, determine how critical the equipment is and the impact it can have to the safety, environmental, business and production of the asset if it failed to function, and assign optimised levels of maintenance.
Software: Effio™
Location: Global
Project synopsis
ABL was contracted to begin building the CMMS data when vessel was in the latter stages of being constructed to assure readiness of an optimised maintenance management regime when the project moved into start-up and subsequent operations.
A lack of internal capability and CMMS build software in-house triggered the requirement for external support. With an already established maintenance management partnership with the FPSO operator in place, combined with our extensive experience and CMMS build software tools that are able to unlock time and cost efficiencies in the project delivery, ABL was selected to deliver this CMMS build.
What we did
- Tag extraction from engineering drawings
- Asset register and functional location hierarchy build
- Equipment classification using ISO 14224
- Equipment criticality assessment and assignment
- Maintenance task assignment, this also included a comparison between the FPSO operators traditional maintenance assignment methodology and their proposed new Blueprint approach to help further refine the content and application
- Further equipment classification to assign flags to tags (Ex, SCE, regulations, SIL, CBM and CHS)
- Alignment of CMMS with external maintenance registers (e.g., PSV register)
- Review of As-Built documentation and update of all required CMMS data following completion of construction
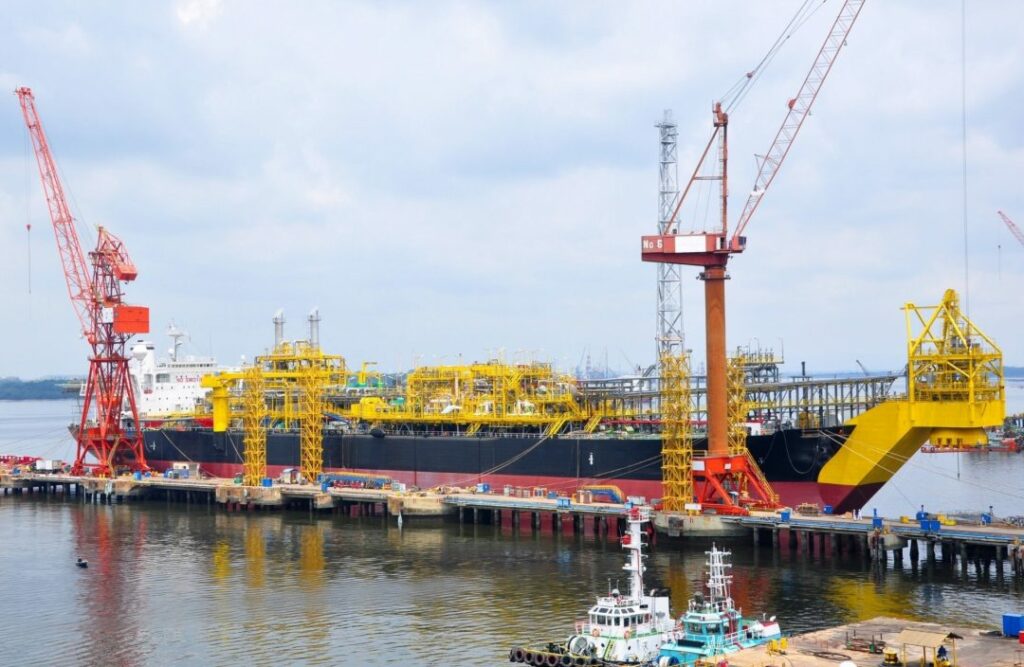
Project deliverables
- CMMS upload files containing the asset register, classification, criticality, and associated maintenance requirements
- Criticality assignment report and justifications
- Initial build and as built documentation such as P&IDs, electrical one-line drawings, lay-outs etc, were reviewed and electronically highlighted to identify those tags that were retained for use within the CMMS and those that were excluded, as well as the main function boundaries
Software used to deliver this project
Effio™ is a cloud-based master build and management of change tool that can replicate our clients CMMS, EAM or ERP environment and provides a user friendly, collaborative, and accessible platform for building, updating, reviewing and approving master CMMS data, assigning criticality, and allocating maintenance and materials to equipment tags efficiently, consistently, and accurately.
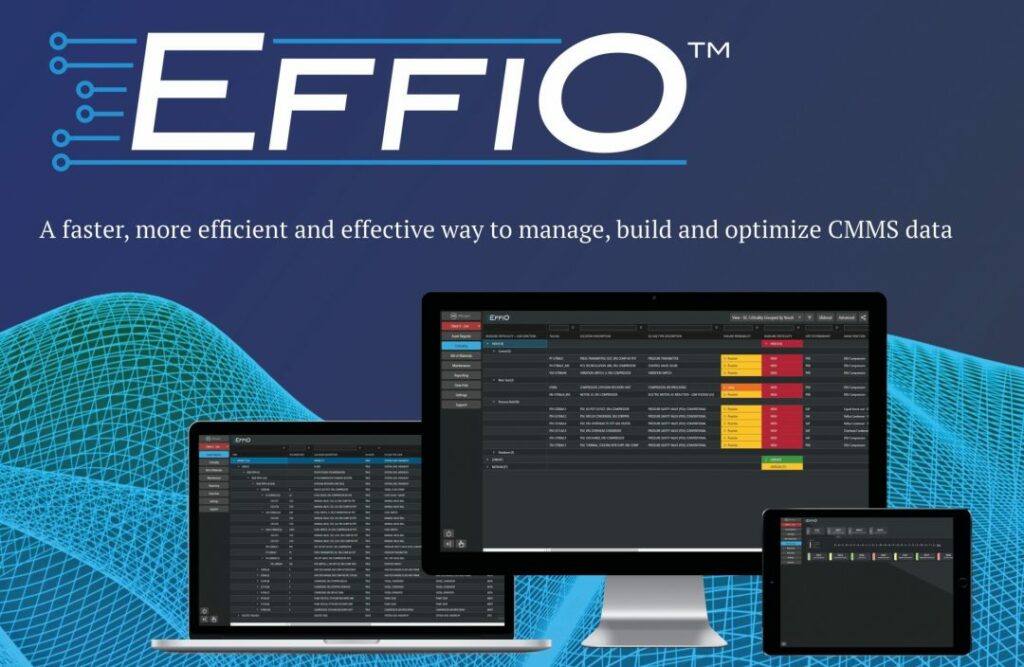
The value we delivered
A cost-effective CMMS build solution
Utilising our established CMMS build processes and software tools, we were able to reduce the project costs by 17% when compared to alternative providers and traditional manumatic methodologies
A clear understanding of the projected maintenance burden
The clients desire to develop the maintenance management regime during the construction of the FPSO provided clear foresight on the maintenance workforce requirements and associated budgets, for better planning, preparation, and controlled expenditure during operations
Assurance of data standardization and consistency
Using our CMMS build software, Effio™ and its built-in data governance rulesets which are customised to align with the client’s CMMS data standards, quality assured data standardisation and consistency was achieved, resulting in load-sheets being delivered to the clients CMMS with zero errors
An accurate digital representation of the FPSO
All maintainable equipment on the FPSO is reflected accurately in the CMMS and can therefore be managed appropriately to mitigate risk and assure reliability
Ability to manage safety critical elements effectively
The identification of safety critical elements and allocation of their maintenance task requirements enables the FPSO operator to manage and mitigate risk, and assure compliance with performance standards and legislation
Optimised maintenance expenditure
Assigning optimised levels of maintenance to the right equipment, at the right time – no more no less enables maintenance expenditure to be truly optimised