M100 Field Maintenance Training
M100 Field Maintenance covers all aspects of equipment maintenance with additional maintenance management theory and practice.
Delivery: Blended course
Duration: 11 week programme, 1 hour virtual, 10 weeks to complete 8 assignments and 1 week Face-to-face classroom
About the M100 Field Maintenance course
The M100 Field Maintenance course covers all aspects of equipment maintenance. It is largely equipment-based, with additional maintenance management theory and practice being covered in the face-to-face week. The design draws on international standards, codes and good practices and includes observations from professionals with 35+ years of experience.
The M100 course takes into consideration that Maintenance staff fall under 3 main disciplines;
- Mechanical
- Instrumentation
- Electrical
It also accounts for Operations staff on the course who are looking to deepen their knowledge of maintenance processes and build their relationships with (office based) support staff.
The key skills and knowledge that candidates will develop:
- An overview of the other Maintenance disciplines to give broadening and potentially facilitate multitasking.
- Detailed knowledge of initial equipment selection, alternatives considered and long term upgrade plans. Handling of obsolescence plays a key role in this.
- Practical details of the equipment they work with, including operating principles, common failure modes and troubleshooting.
- Methods of identifying optimisation and improvement opportunities, and practical ways of implementing changes to bring the improvements about.
- How they can interact with staff in other departments who are also closely involved with their equipment, and how diverse departments can cooperate more closely.
How much does the course cost?
We keep pricing available on request as we like to discuss your needs and expectations in order to deliver a unique training experience.
Who should attend?
This course is suitable for field and office based production operations personnel, and those in adjacent departments who require broadening.
Staff at all levels may apply, from new intake including incoming graduate staff to experienced hands.
The course supports the development of crafts, trades and technical professionals by enhancing knowledge of their role within an operating environment whilst laying a solid foundation of the skills and knowledge required to enhance their work.
How many people can participate?
We have set the minimum number of candidates to 12 and maximum to 20, however, if you would like to run this course with groups of more than 20, please contact us using the form below and we can accommodate this with multiple back to back in person training weeks.
Course structure
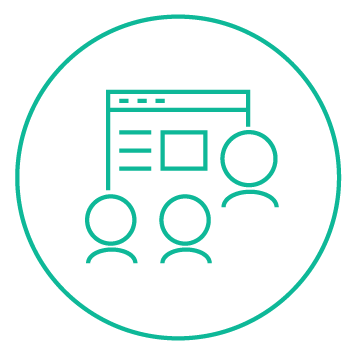
1
The course begins with an online introduction of candidates and facilitators, highlighting the course expectations.
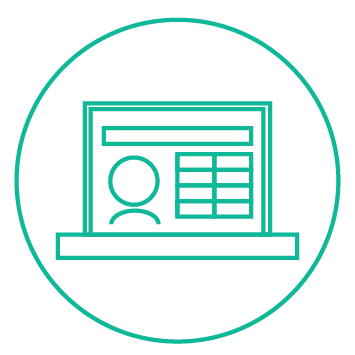
2
Candidates are given eight assignments spread over ten weeks and selected based on the needs of each candidate.
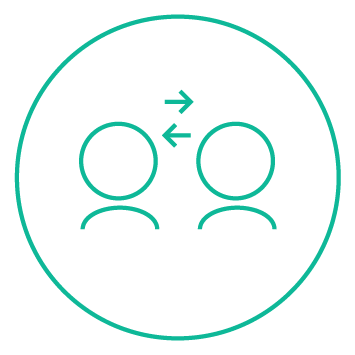
3
The workshop is a five day event and will include facilitator-led interactive learning sessions, group activities and candidate teach-back sessions.
More ABL Training courses
Comprehensive Risk Management: Combining Quantitative Risk Assessment (QRA) and Barrier Risk Management (BRM)
As Low As Reasonably Practicable (ALARP)
Barrier Management
Quantitative Risk Assessment (QRA)
Hazard and Identification (HAZID)
Hazard and Operability (HAZOP)
Effective Risk Assessment
Process Safety Management (PSM)
P100 Field Production Operations Training
Related ABL Training content
Global maintenance training and development for a multinational organisation
4 ways to upskill and grow your maintenance team
Submit the form below to enquire about the M100 Field Maintenance course or any other ABL Training