4 ways to upskill and grow your maintenance team
Following two years of working through a pandemic, it’s no surprise that there are growing skills gaps emerging across companies – as budgets have been cut, teams have been forced to downsize, and with that, knowledge and experience has been lost.
Many maintenance teams across the globe have felt this pressure, and there’s now a rising need to upskill and fast-track competence in order to achieve performance targets.
From identifying specific training needs, to focusing on deepening and broadening your team’s skills, he has shared valuable insights in this blog post…
1. Identify your specific needs before selecting training solutions
“A mistake I see made time and time again is organisations spending a lot of money sending their team on training courses before they identify where improvements are required – but it needs to be done the other way around in order to be effective.
“If you’re considering upskilling your team, the first thing you need to do is identify any important skills gaps. This will enable you to seek out specific and highly relevant opportunities for individuals – and give you the greatest chance of effectively plugging a skills gap, and enhancing your team’s performance.
.png)
“Look at the subject matter involved, understand what it is, understand where the gap is within your team, and then identify training you will actually benefit from. You could find a specialised training course that is perfectly aligned with your needs, or perhaps the skills gap could be plugged by simply engaging with a highly experienced member of the team, and facilitating others learning from them.”
2. Deepen your team’s skills within their own specific trade
“An important part of upskilling your maintenance team is deepening each individual’s understanding of their own trade and ensuring they maintain a high level of knowledge as the trade changes over time. In maintenance roles in particular, this can often fall by the wayside due to the busy and often reactive nature of the job – but it is fundamental to enhancing your team’s performance, and ensuring mistakes or inefficiencies don’t become the norm.
“An effective way of monitoring this, and identifying any weak areas in your team, is through conducting regular technical skills tests – physical, hands-on tasks with team members put on the spot. We have helped many companies roll this out and it always an extremely valuable exercise for both leaders and tradespeople – as it allows you to zone in on where knowledge and skills need to be refreshed, to make impactful changes.”
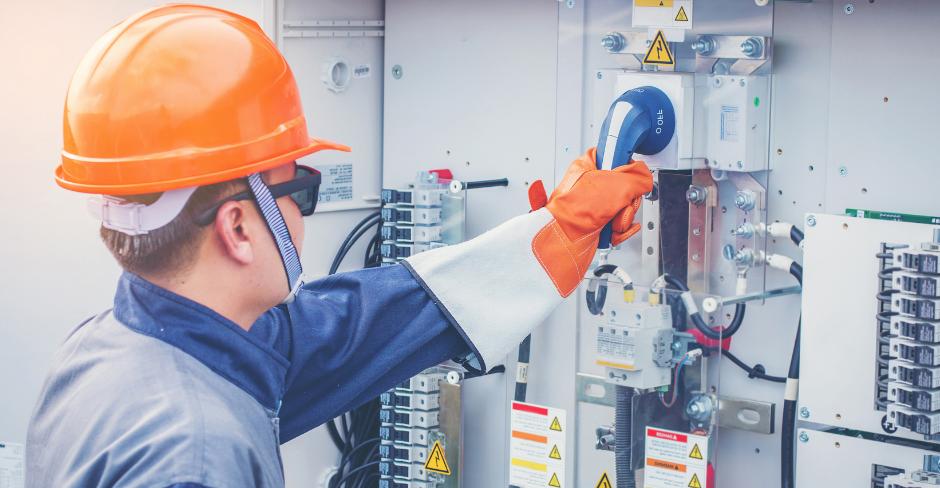
3. Broaden your team’s knowledge
“While deepening your team’s technical skills is crucial to growing your team, it is also important to broaden their knowledge too. You ideally want your team to become more aware of the context and situations they’re working in – this could involve learning about supporting trades or disciplines, or improving their non-technical skills in areas such as analytical techniques, risk assessment, leadership and decision making.
“Someone working on a piece of equipment will generally be competent in their job, but lack the awareness of the many other interactions between people and equipment that are occurring around them, and this is often why mistakes are made and plant performance is compromised.
“At ABL, I’ve recently developed a course that is designed to broaden a team’s understanding of the whole maintenance process, so they have a foundation level of knowledge across a wide range of skills relating to maintenance and operations management. This helps to create a better, higher-performing maintenance team and ensures that you are more resilient to change.
“By the end of the course, students should be able to identify the main maintenance processes that occur from start to finish, and gain a deeper understanding of how each step applies to their own job. It supports the development of trades and technical professionals by enhancing knowledge of their role within an operating environment whilst laying a solid foundation of the skills and knowledge required to enhance their work.”
4. Set an example to ensure that learning is continuous
“I see time and time again that a lot of managers are not dedicated to their team’s professional development because they “don’t have time”, as a result of cost and time pressures imposed upon them. However, this goes back to that age old saying “Failing to plan is planning to fail”. Or “if you think training is expensive, try an accident” If you fail to keep up with your team’s professional development then you cannot be shocked when mistakes are made, or performance dips.
“It’s also important to lead by example and instill a culture of continuous improvement. If you yourself focus on enhancing your own skills, keep up-to-date with technology advances, and participate in training, your team will follow and take more of a proactive interest in their own learning and development.
“Practicing is a fundamental part of upskilling. Often individuals are sent off to a training course as a “tick box” exercise, and nothing they learn is implemented within their day-to-day work.
“You need to identify skills gaps, find the best suited training courses, but most importantly, continually practice these learnings in daily operations, to achieve lasting change and enhanced performance.”
Highly recommended courses for your operations and maintenance teams
Courses designed by subject matter experts and instructors with extensive hands-on asset management, maintenance, integrity, CMMS utilisation and inventory management experience: