Global maintenance build and strategy optimisation
Project Objective: To achieve safety integrity assurance and performance excellence through a data-driven maintenance improvement project.
Client: Oil and Gas Operator
Asset: 30+ onshore and offshore production facilities
Duration: 4 years
Location: Global
Software: Effio™
Project synopsis
Without a meticulously designed and executed maintenance management regime, plants are subject to increased risk of equipment failure, loss of production, and excessive maintenance costs – which will directly impact the safety integrity and performance of the plant.
To truly optimise the client’s maintenance and materials regime and unlock the associated benefits that come with it, it was key to build this regime using reliable, structured, and quality master data. Realising the need to have this in place, ABL was contracted to deliver a global maintenance optimisation project where we were tasked with enriching the CMMS data and optimising the maintenance management regime, and associated spare parts in excess of 2 million equipment tags.
The challenge
To assure the right level of preventative and predictive maintenance and inspection, on the right equipment, was being done with the right materials, at the right time – no more, no less. Achieved through:
- Having the means to operate safely, by having complete visibility of what equipment they have, how its classified and risk ranked, how and when it should be maintained, and the materials that are required to do this
- Applying best-in-class maintenance strategies at an optimum frequency to mitigate failure, reduce risk and optimise cost
- Consolidating the client’s approach to maintenance and integrity management by migrating into one standardised global CMMS solution
What we did
The ABL team were contracted to deliver the review, enrichment, and optimisation of the client’s global approach to maintenance and integrity management. This included:
- Equipment identification: to ensure all equipment that requires maintenance was in the CMMS, by establishing and implementing the data standard
- Equipment classification and criticality: to ascertain how critical the equipment’s function is to the asset’s production and safety integrity, to determine the optimal maintenance requirements
- Equipment strategies: utilising an FMECA based approach and discovering existing pockets of maintenance excellence to apply learnings across assets, ensuring the optimum level of maintenance is assigned to equipment whether that be assurance, preventative, predictive, or contingency
- Equipment task lists: providing high-quality task lists, and a consistent approach to how maintenance is performed by the maintenance team
- Equipment materials: populating the CMMS with the correct BoMs to ensure the right spares parts are identified to execute the maintenance with consumable and contingency spares
- CMMS implementation: Hassle free CMMS upload templates adhering to the change management process
The results
Having complete visibility of their equipment, and how important it is, has been instrumental in building the foundations for achieving maintenance excellence. The client now has confidence that they are maintaining equipment at an optimum level and ensuring the risk profiles are still being managed.
As a by-product to the safety integrity and reliability benefits, this client also benefited from some significant cost savings, including:
- Savings of over $9M per year through the cleansing and net removal of 290,000 tags in CMMS that were duplicates or decommissioned equipment, additional critical tags were also added
- Savings of over $21M per year by rationalising 198,000 annual planned maintenance hours
- Savings of $8.7M per year through optimisation of annual planned maintenance work orders
- Savings of $18M on planning and efficiencies gains through enrichment of 147,000 Maintenance BoMs
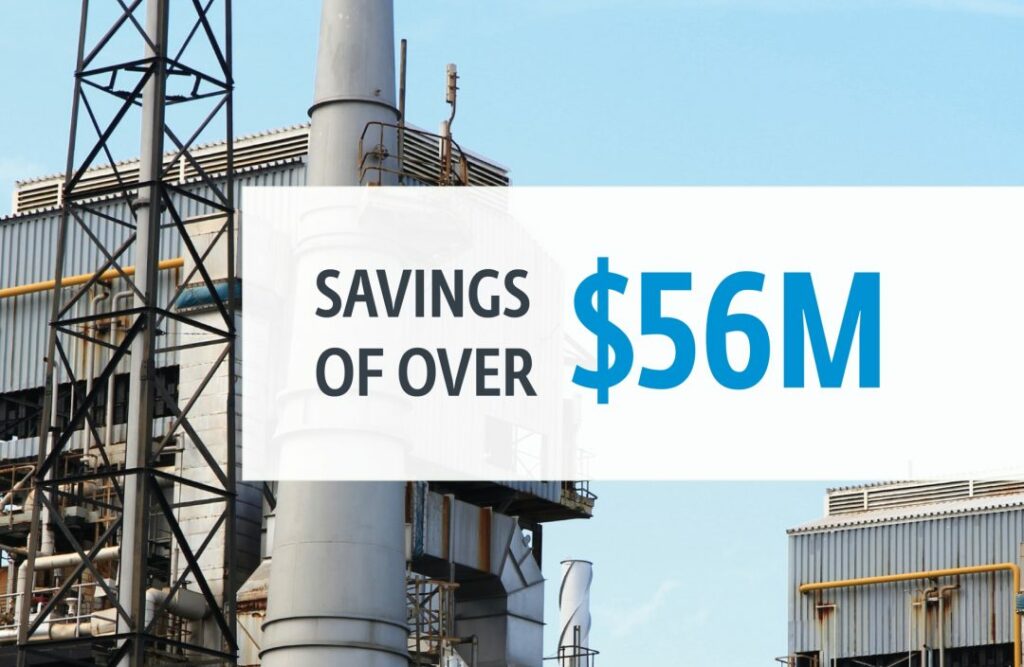
“Plant reliability is one of the most noticeable outputs of this project; not only are we setting record reliability statistics, but we are achieving this with optimised levels of maintenance, done at the right time, in a globally consistent manner.”
Director of Maintenance, International Energy Producer
Get in touch
By filling in the form below, you can speak to one of our experts to learn more about our solutions, request a quote or book a software demonstration.